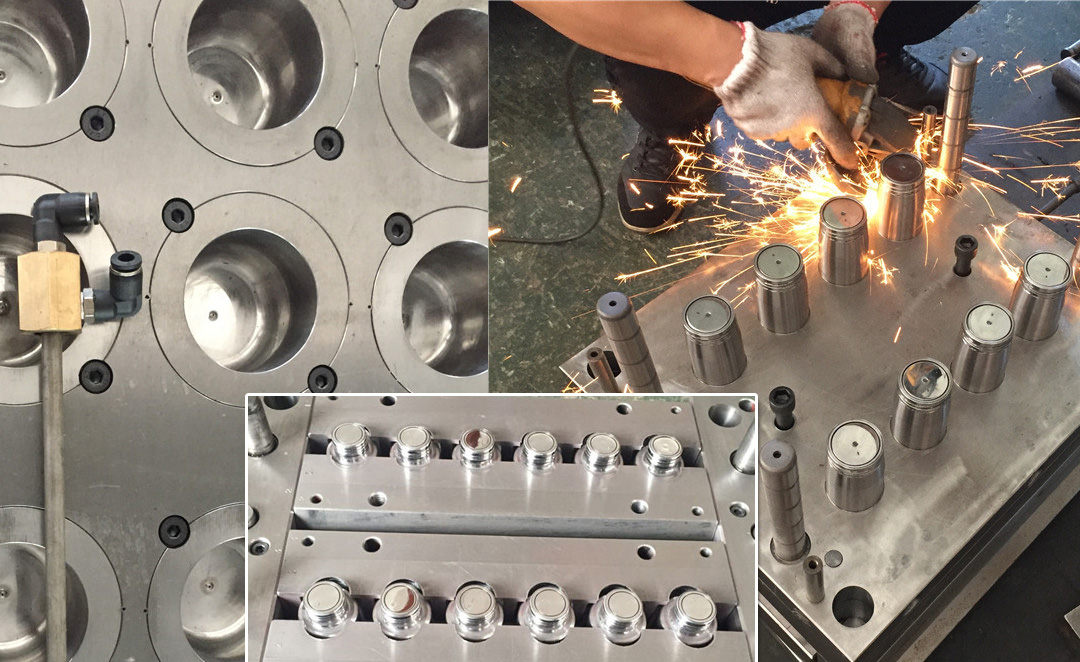
Explanation of detailed knowledge points of rubber mold design in bottle cap mold factory
Flip Top Caps Mould in China
Automatic flip top cap mould structure is more difficult than normal caps, the mold ejection system is special and have double steps. the cap closing success rate is very important to the Mould.
Shuanghao is the cap mould maker in China, who can make 24 cavities flip top caps mould with automatic closing system. Automatic production equipment is much more safer than human made. And it will help save cost in employee labors. Full automatic is international trend toward. If you want to improve your injection equipment, welcome contact me free. We are flip top caps mould China and looking for more and more partner all over the world.
After the plastic bottle cap mold is installed, the mold must be preheated before mold trial. There are roughly two methods for mold preheating. It uses the cooling water hole of the mold itself to pass in hot water for heating. At present, there are a large number of mold heaters used at home and abroad, which is a good method for mold heating. The second is the external heating method. That is, the cast aluminum heating plate is installed on the outside of the mold, and the heating is carried out from the outside to the inside. This method heats up quickly, but consumes a lot of heat energy. It is more suitable for the cold winter in the north.
For plastic bottle cap molds, the heat of the injection material can be used to increase the temperature. The use of raw materials that are not difficult to inject does not require mold preheating. However, for large and medium-sized molds, the molten material is forcibly injected into the cavity with separated temperature materials and high pressure. Although it is also possible to obtain test-molded parts, it actually causes serious damage to the mold itself and wastes energy. Due to the large internal stress and serious deformation, the size of the obtained part is very unstable, which brings trouble to the inspection of the size of the part. Therefore, this method should not be adopted.
When the mold is preheated after installation, the injection barrel is also heated. When both temperatures meet the requirements, that is, when the mold temperature reaches 30-60°C or more. When the plastic in the barrel is in a molten state and is uniformly plasticized, it is deemed that the temperature is appropriate, that is, the test mold injection conditions are available, and the test mold can enter the test injection stage.