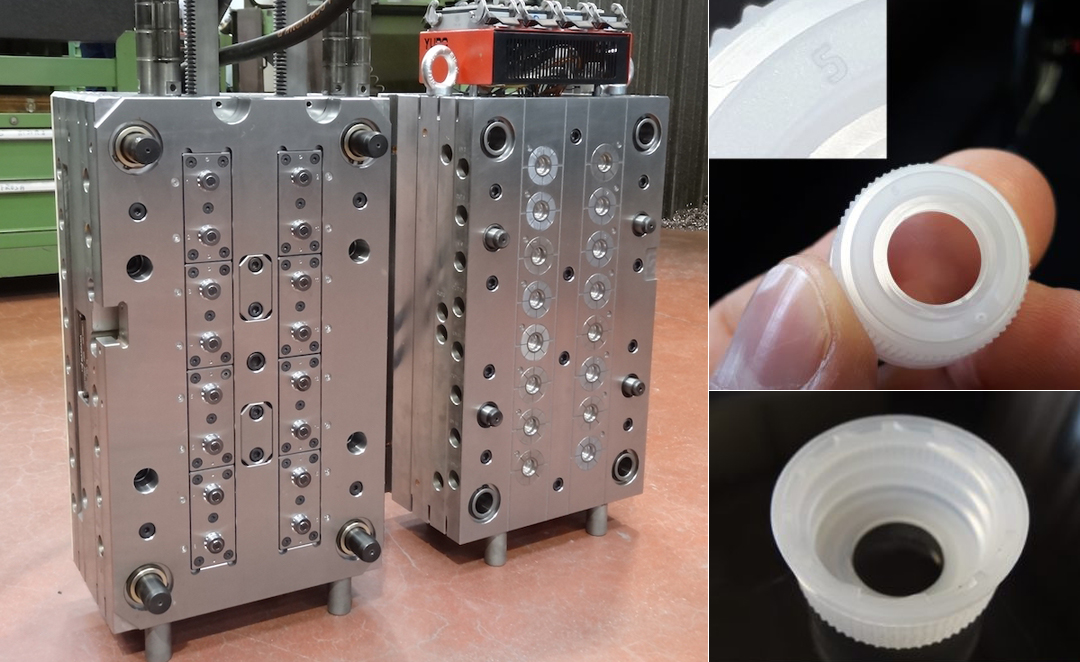
The injection system Shuanghao cap mould
For the mold design discussed, it must be emphasized that the filling of molten plastic material was also simulated to avoid cold joints, air entrainment, and restriction of ovalization. After the simulation, the hottest areas can be highlighted to optimize temperature regulation and reduce the expected cycle time. Finally, the hot runner injection system was selected.
From technical office to tools
After the mold design phase, which lasted about 15 days, the activity moved to the mold shop, where Makino’s 4-axis and 5-axis high-speed machining centers (programmed using CAM Cimatron from 3D Systems) were operated. Especially high-speed turning and milling; then rectification."
In particular, a system was designed and built to quickly adjust the line start time of all impressions, even without disassembling the mold from the printing press
The main difficulty is to ensure the highest possible accuracy so that the indentations inside the matrix (16 in total) are exactly the same, or more precisely, the dimensional tolerance is 5 percent of a millimeter.
"For many years, I have been focusing on the design and construction of multi-cavity molds. This is also due to the use of the OGP system, which is an optical three-dimensional metrology system that can certify printed parts to ensure complete interchangeability and follow-up Replacement with absolute repeatability over time». In related cases, in order to ensure the correct sequence of the various stages of the molding cycle and ensure the correct function of the production stage, different types of sensors are used to check the complete extraction and unscrewing system. Work This is followed by wire cutting, especially for the implementation of raised rings to facilitate the function of the injection point.