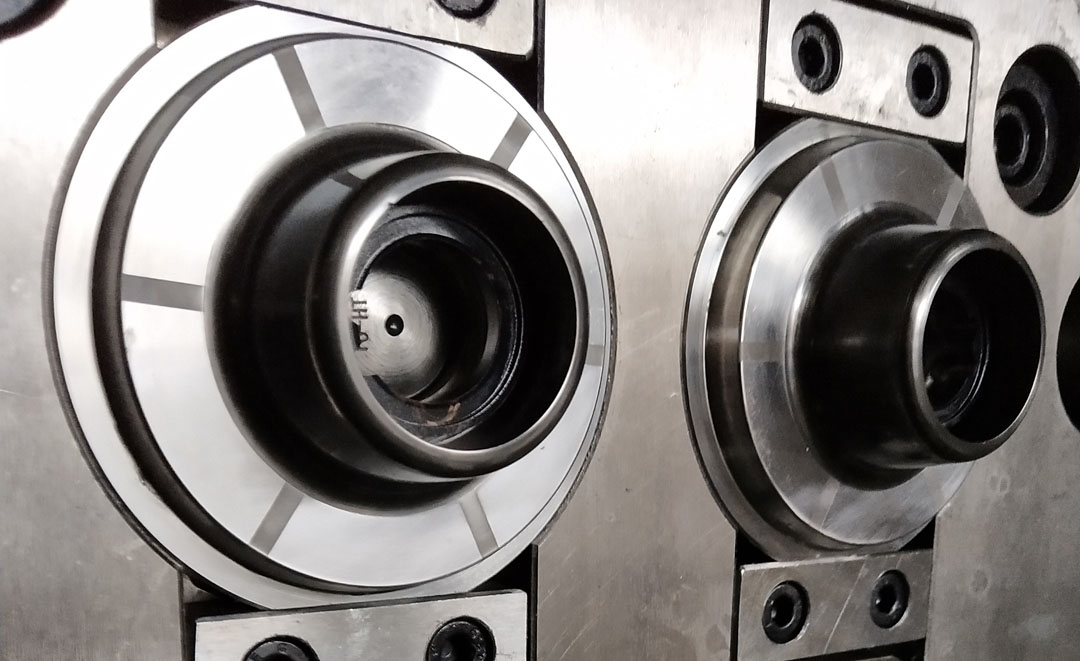
what-are-the-design-elements-of-the-bottle-cap
Bottle cap molds are now widely used. In our daily life, they are widely used for multi-packaging work such as edible oil, beverages, sugar cubes, medicines, etc. The bottle caps have relatively consistent quality standards and caliber parameters, so Said that the production and manufacturing of bottle caps is relatively standard. It can be said that the blowing mold determines the shape of the plastic bottle, and the preform largely determines the quality of the plastic bottle. Needless to say about the importance of the plastic bottle.
Considerations for the design of plastic bottle cap molds. When planning the needs of bottle cap molds, according to the shape, accuracy, size, skill requirements and production batches of plastic parts, consider the following aspects when planning the mold:
a. Number of cavities and placement method: bottle caps are produced in large quantities as packaging containers, and one mold with multiple cavities should be selected. Considering the clamping force of the existing injection molding machine, the amount of injection, and the accuracy and economic factors of the cap, it is determined as 1 mold 10 cavities, the cavity placement method is "in-line".
b. Pouring system planning: According to the layout of the plastic parts, the mold is planned to be a three-plate type with point gates. The gates are set in the center of the top of the plastic parts. The point gates can significantly advance the shear rate of the melt and make the melt viscosity A large drop is conducive to mold filling, and it is especially useful for melts that are active in shear rate such as PE. And as a packaging container, plastic parts have high requirements for appearance quality and small residual traces on the point gates, which can ensure the surface quality of the plastic parts. The gate will automatically be broken during demolding, which is convenient for ending the automation of the product production process and increasing the production power. , Increased economic benefits. The non-balanced pouring system is selected, the cavities are placed compactly, and the mold standard is reduced. In order to make all the cavities evenly filled together, the selection method is adjusted manually to balance the gate standards of each cavity. Use cold slug to store forward cold slug.
c. Cooling system planning: The mold temperature scheduling system for bottle cap molds directly affects the quality and output of products. For the cooling power of the traveling cavity, a cooling circuit is selected. The inlet of one circuit is located near the exit of the other circuit; it is bundled according to the shape of the plastic part and the mold layout, and the fixed mold cooling channel diameter is φ12mm, which is connected with the external hose to form a circulating cooling . The diameter of the core of the movable model is relatively small, and the steel pipe cooling method is used. The soft copper core rod with good thermal conductivity is pressed into the center of the core, and one end of the core rod is extended into the cooling water hole for cooling.